How Pre-Manufactured Structures Are Shaping Commercial Spaces
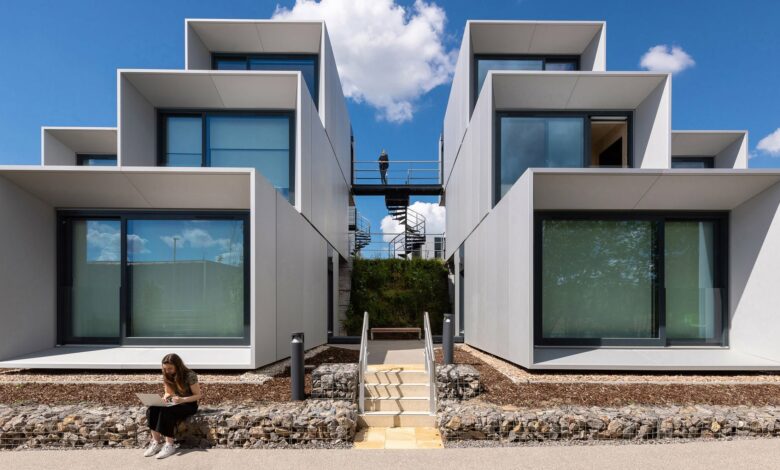
As the 21st century unfolds, a significant shift is becoming evident in the construction industry. Pre manufactured buildings initially dismissed as a fringe innovation, are increasingly gaining acceptance in the realm of commercial spaces. This form of construction integrates advanced technology with proven building methods, promising to revolutionize the future of commercial architecture.
The Rise of Pre-Engineered Buildings
Pre-engineered buildings, also known as modular or prefabricated buildings, are assembled off-site and transported to the building site for final installation. These structures are not a new concept, but recent design, technology, and sustainability advancements have fueled their growth and application within the commercial sector.
These types of buildings have long been associated with residential structures, but they are no longer limited to such confines. The commercial sector is now seeing an influx of these innovative construction solutions, extending to office buildings, retail spaces, and even high-rise skyscrapers.
The Advantages of Pre-Manufactured Buildings
There are several compelling reasons why a pre-manufactured building is proving to be the next big thing in commercial construction.
Cost and Time Efficiency
One of the most significant benefits of pre-manufactured structures is the cost and time efficiency they bring. Off-site construction takes place in controlled environments, minimizing the impact of weather delays and enabling simultaneous site work and construction. This leads to a reduced build time which inherently cuts down on costs.
Flexibility and Customization
These buildings offer a high degree of flexibility and customization. Designs can be easily tweaked to suit unique requirements, making it possible to create spaces that accurately reflect a company’s brand and operational needs. This adaptability extends to future modifications, with modules that can be added, removed, or reconfigured.
Sustainability
Pre-manufactured structures are stepping up in an era where the call for sustainability is louder than ever. With precise construction techniques that minimize waste and an ability to incorporate energy-efficient designs and materials, they can significantly reduce a building’s carbon footprint.
The Role of Technology
The integration of technology in the pre-manufactured building process is pivotal. Advanced software programs are used for precision design and fabrication, reducing errors, and enhancing the overall efficiency of the construction process. Furthermore, the use of technology can aid in virtual tours, allowing clients to walk through a digital representation of their space before it is physically built.
The Future of Commercial Spaces
Pre-manufactured structures and buildings are not just a passing trend but a viable solution to the many challenges that traditional construction methods present. The adoption of these structures within the commercial sector is expected to increase, driven by their inherent advantages and the evolving needs of the commercial market.
For instance, the ongoing shift towards flexible workspaces and remote working models necessitates structures that can adapt quickly. With their inherent modularity, pre-manufactured structures can accommodate these changes, reinforcing their value proposition in the commercial construction sector.
Conclusion
As you look to the future, it is clear that pre-manufactured buildings are more than equipped to meet the evolving demands of the commercial construction sector. They present a unique blend of efficiency, flexibility, and sustainability that traditional methods struggle to match. Their rise is not just reshaping the commercial construction landscape; it’s offering a glimpse into the future of built environments. With these buildings, the future of commercial spaces seems more sustainable, adaptable, and exciting than ever.